Advanced process control is today one of the main branches of the so-called fourth industrial revolution(Industry 4.0). It has been emerging for several years now as an alternative to optimize the way plant control loops operate. This is the use of control strategies different from those of classical control that can offer better performance in the operation of equipment. The designer is responsible for analyzing the variables to be controlled (level, pressure, temperature, flow) and the characteristics of the type of process to choose the strategy that best suits the control objectives. The use of these strategies offers improvements in aspects such as increased production capacity, reduced energy consumption, increased quality standards of the final product, among others.
Contextualization of the current loop control standard:
The loop control strategy that is standard today, and has been so since the emergence of automation, is PID control (proportional, integral and derivative control). This strategy has been around for over 100 years (developed by Elmer Sperry in 1911) and such a control can be found in almost any industrial plant.
The performance of PID control depends primarily on the loop design (selection of the control element and the process variable). Also the characteristics of the process where the control will be installed. The designer must take into account these aspects and choose the characteristics of PID control that best suit the process. Also, after installing the control, you must complete a tuning process. Where the algorithm is tuned to ensure stable behavior of the process at the operating point.
However, there are scenarios of PID control in which after the end of the tuning is not possible to achieve optimal operation of the equipment. There are even cases in which the PID control is not possible to achieve acceptable behavior of the equipment variables. The user is forced, in the worst case, to have to operate the equipment in manual mode. These scenarios cause, of course, losses in production capacity, energy consumption or quality of the final product.
This limitation of PID control is justified in the capacity of the algorithm itself, which often cannot meet the requirements of the process in which it is installed. It is for this reason that, in response to this condition, multiple alternatives to classical PID control arise in the context of automation. These are designed to improve the performance of the loops and to achieve optimal operation of the equipment. They are called advanced control strategies.
Advanced control in Custom Control Colombia:
Custom Control Colombia has an engineering team specialized in the design and implementation of advanced control strategies. This has experience in the implementation of multiple types of strategies. Whenever you come to a new plant, our team conducts an analysis of the characteristics of the process and the experiences of the operation. This is in order to identify which parts of the process can be improved with advanced control and which types of strategies are best suited to the needs of the process. Our clients acquire with Custom Control an ally that is permanently involved in the process of identifying new opportunities for improvement in the field of control(continuous improvement).
Advantages of advanced control implementation:
The most representative advantage of advanced control is the ability to make the control system more robust and versatile to maintain a team within stable operating parameters. The system user sets target values of equipment variables and control is responsible, safely, to bring and maintain the equipment at that operating point. This advantage generates multiple benefits, as summarized below:
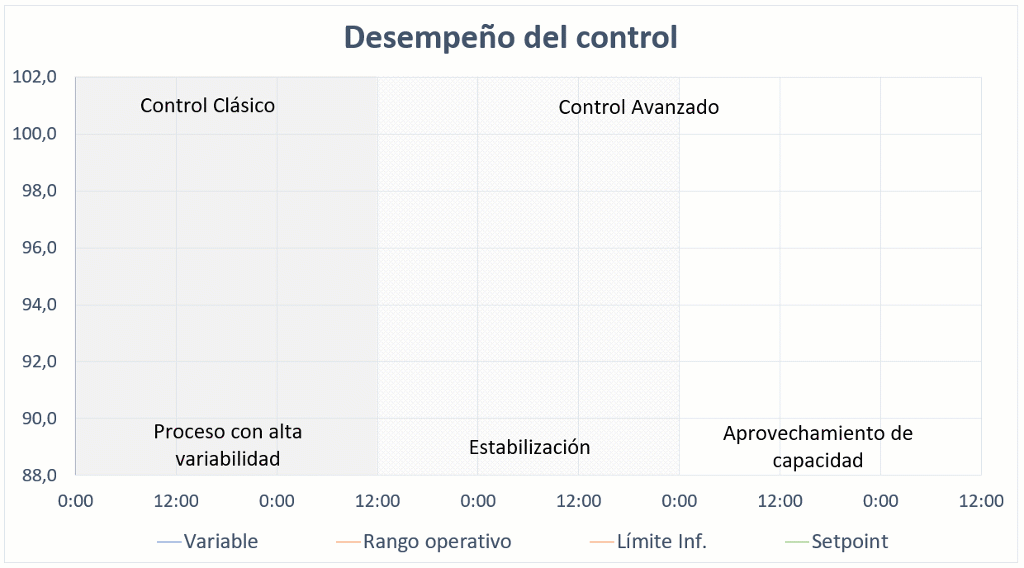
Optimal use of equipment capacity:
When a team is found that the PID control does not have a good performance, it is common to see that the control fails to maintain the process variables in a stable value. The operator assigns target values and the control fails to maintain the plant at these points. On the contrary, constant variations are seen and it is often required that the operator must make manual actions to try to bring the plant to a stable point. It is in these scenarios where the maximum production capacity of a piece of equipment cannot be used. Because of the risk that with maximum capacity variations cause alarms and detrimental process events. The operator is forced to decrease production to the point necessary for the equipment to operate without failure.
The advantage of advanced control is that with the application of such a strategy, process variations can be minimized or eliminated. This also achieves a more stable behavior of the equipment. This allows the operator to increase the production capacity without the risk of causing process events. The nominal production capacity can then be used.
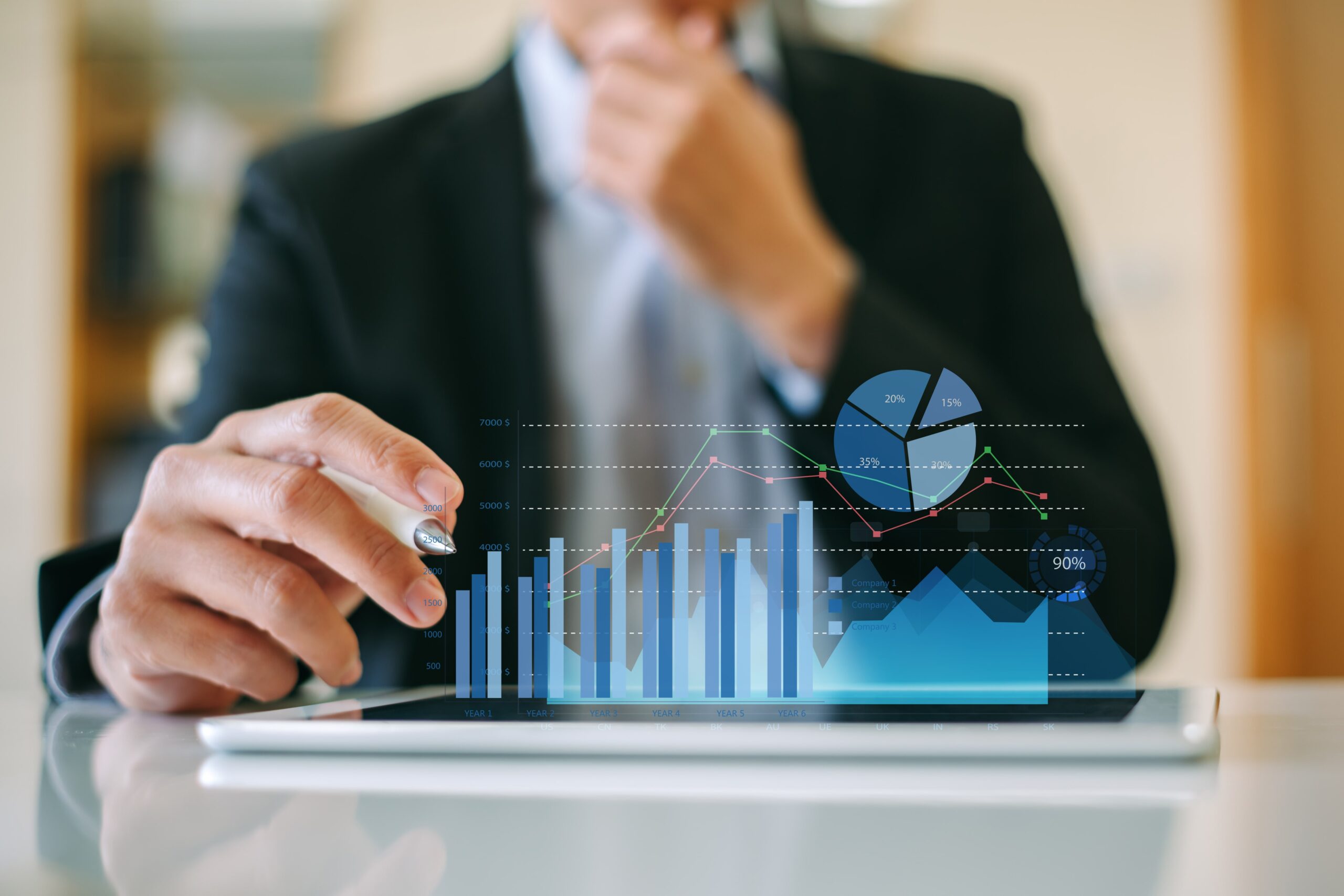
Decrease in energy consumption:
This is also an advantage of increased stability and decreased variability. With the advanced control it is possible to bring and maintain the equipment to its maximum energy efficiency point. This minimizes over time the amount of energy required to generate the final product.
Increased quality standards:
This is also a benefit of the control’s ability to maintain process variables in stable conditions and close to target values. As long as a piece of equipment can operate under these conditions, it is expected to operate in accordance with its design parameters, thus providing a final product in optimal quality conditions. Over time, out-of-specification end-product events are minimized or eliminated.
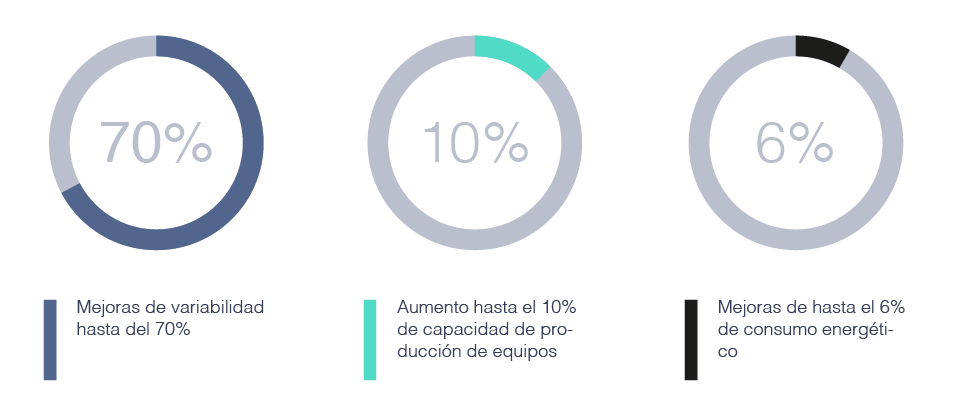
Value Added:
In relation to the design and implementation of control strategies. Our company uses a methodology that is designed to minimize or eliminate all risks involved in the installation of such a strategy. The objective is that prior to installing the strategy in the plant, all the necessary engineering activities must be carried out to ensure reliable and robust performance. In summary, the stages of the methodology are as follows:
- First, before starting with the design of the strategy, a thorough analysis of the engineering and current state of the process is made. This is to identify the control needs. In addition, an analysis of the state of the plant’s loops and interviews with operations personnel are conducted. This is to understand what are the critical variables of the plant and where you could achieve greater benefit with an advanced control strategy.
- Second, with the engineering information, a simulation model of the process section where the control will be installed is designed. This is a virtual plant and serves to carry out all the necessary tests of the advanced control strategy. The model must be sufficiently accurate to approximate the actual behavior of the equipment in plant.
- Third, multiple control strategies are tested in the virtual plant to find the strategy that best suits the control needs. Once a strategy is chosen, tests are performed in different scenarios also with customer support. This so that there is confidence in the performance and characteristics of the control even before installation in the actual plant system. The end result is a robust design that meets the control needs and minimizes implementation risks.
- Fourth, the strategy is finally installed in the plant. In view of the fact that the system has been tested in various operating scenarios, installation and commissioning tends to be a short stage. The time is more focused on the execution of performance tests, fine tuning of the control and training of all personnel involved in the operation.
Experience:
Within its portfolio, the most representative control strategies in which Custom Control Colombia has implementation experience are:
- Fuzzy Control.
- Model Predictive Control (MPC).
- H-Infinite.
- Control with Game Theory (Game Theory – Population Dynamics).
- Adaptive Control.
- Internal Model Control (IMC – Internal Model Control).
- Neural Network Control.
Regarding the processes in which our team has installed advanced control strategies, the oil & gas industry stands out:
- Treatment tanks (FWKO tanks, Gun Barrels, storage tanks, Skim tanks).
- Two or three phase separators.
- Heat exchangers.
- Water treatment plants (flotation cells, scale filters).
- Pumping plants and water injection plants.