Custom Control Colombia ‘s advanced control implementation experience began in 2016. However, our specialists have more than 10 years designing and implementing control strategies for the OIL & GAS sector. The result is a robust design methodology that is intended to guide the process of development and validation of control strategies.
This methodology consists of nine steps:
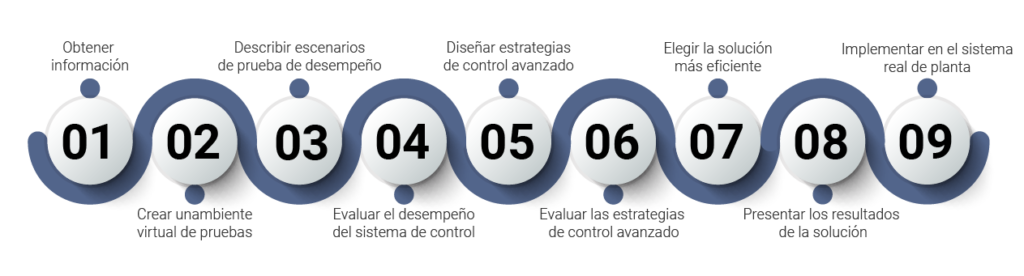
- Obtain information on the process and the customer’s needs. In this step, a system information survey, an analysis of the state of the process and interviews with the personnel involved in the process are carried out in order to recognize control needs.
- Create a virtual test environment. This consists of a simulation model and the emulated control platform. The objective here is to create a simulation environment (virtual plant) that serves to test the control strategies.
- Describe performance test scenarios. This step defines the objectives of the control strategy and the process scenarios in which those objectives must be met. The strategy must succeed in meeting those objectives in each of the scenarios.
- Evaluate the control system prior to the implementation of advanced control. For this purpose, the virtual environment of the process and the described scenarios are used. The objective is to identify the response of the current system to each of the scenarios and how it could be improved with the advanced control strategy. This analysis gives an answer of the current control context.
- Design a series of advanced control strategies and implement them in the virtual test platform. With the results of the analysis up to this stage, multiple control strategies are selected for testing in the virtual plant. The objective is to have multiple options available in order to identify the strategy that works best.
- Evaluate the advanced control strategies in the different test scenarios described. The strategies are tested in the different operating scenarios and their performance is compared by evaluating how well each meets the design objectives.
- Choose the solution that performs best in the test scenarios. With the result of all the tests, the strategy that best suits the process and has the best performance to meet the design objectives is selected.
- Present to the customer the simulation result with the virtual plant and the selected control strategy. In this step the customer is shown the design result and the performance of the control in the test scenarios. The customer can then check the operation of the control before the actual plant implementation.
- Implement in the actual plant system. The last step is to implement the control strategy in the plant. This normally does not require system shutdowns. The strategy is activated, fine tuning is performed, and a monitoring and testing stage is entered.
As a result of the application of this methodology, advanced control strategies have been successfully implemented in different processes. For example, Population Dynamics in water plants, Fuzzy Control in injection systems, optimization methods (two-phase simplex) in distribution systems, among others.
Population Dynamics in water treatment plants:
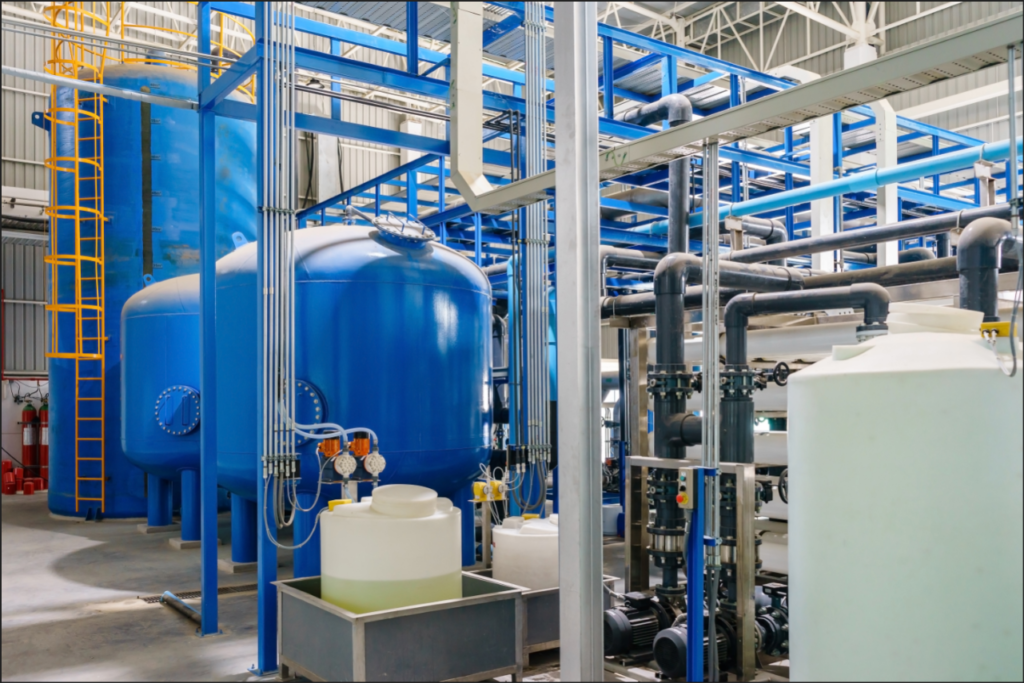
Water plants are widely used in the OIL & GAS industry for the separation of oil particles and solids from water. There are multiple types of plants depending on the type of crude oil being treated. In general, the elements and equipment that can be found in a plant are:
- Flotation cells.
- Scale filters.
- Control elements (control valves and frequency variators).
- Measuring elements (flotation cell level sensors, level sensors in the oil compartment, flow and also pressure measurements at different stages of the plant).
The main objective of the control strategy in water plants is to maintain stable process variables that directly affect the quality of separation (oil levels in the oil compartment, flotation cell levels, among others) and be a little more lax in those variables that have less interference in this objective (inlet flows in the cell, output of water transfer pumps, operating pressure of scale filters). For this reason, Custom Control Colombia designed and implemented a multivariable control strategy based on Population Dynamics. This allows a collaborative work of the control elements, seeking to ensure the lowest variability in the main variables of the water treatment process. As a result, a greater operational continuity, better water quality at the output of the plants and an increase in their autonomy were achieved.
Fuzzy Logic in water injection systems:
A water injection system usually consists of a set of booster pumps and injection pumps. The purpose of the booster pumps is to maintain a suction pressure in the injection pumps. The main (injection) pumps are responsible for increasing the pressure to the necessary values so that water can be injected into wells intended for this purpose.
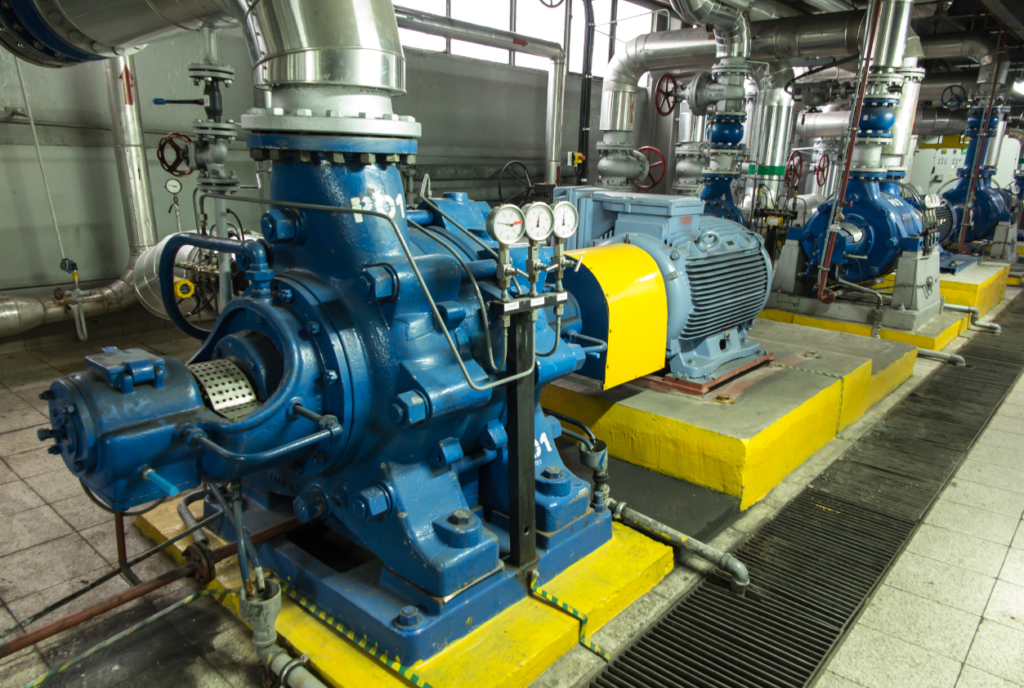
A consequence of cascading between booster pumps and injection pumps is that these systems tend to be very susceptible to pressure disturbances. It is common that the shutdown of a booster pump or injection pump can cause a total system output, and in the worst case damage to piping or equipment. Because of this, it is normal for most injection pumps to be fitted with variable frequency drives. This allows the operator to adapt the pumps to the condition of the booster pumps, the injection wells and the availability of electrical power. However, there is a risk that in the event of a pump shutdown, the operator may not be available to avoid a general shutdown. This is precisely where the advanced control strategy applies. The objective of this strategy is that in the event of pump shutdown, well pressurization or low pressure of booster pumps, rapid action is taken to ensure operational continuity.
Moreover, the advanced control strategy should not allow rapid increases in frequency, as it can trigger electrical protections or cause breakdowns in hydraulic lines. That is why Custom Control Colombia designed a control scheme based on fuzzy logic(Fuzzy Logic). It is achieved with this strategy that the control acts quickly to lower frequency in pump shutdown events and slowly in events that require higher frequency. The result of implementing this strategy in injection systems is to increase reliability, operational continuity and autonomy of the equipment.
Two-phase simplex for fluid distribution systems. Use case in Skim Tanks distribution systems to water treatment plants. :
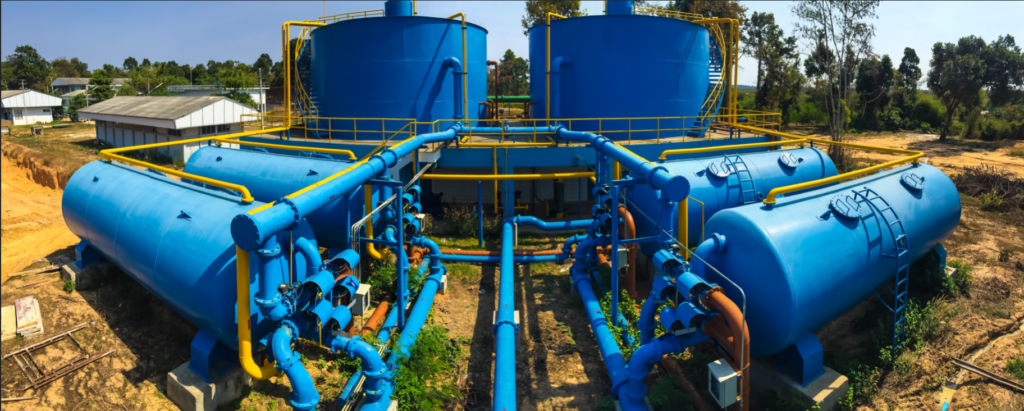
In an OIL & GAS production plant, fluid distribution can occur at various stages of the process. For this particular case, the transfer of fluid from the Skim tanks to the water plants will be analyzed. Where, the operator must periodically choose which water plants should receive more or less fluid, depending on the removal efficiency, capacity or availability of equipment at each water plant. On the other hand, the operator must always maintain a minimum fluid to be treated in water plants; thus avoiding a high level in the SKIM TANK.
Based on this information, an optimization problem was proposed. The cost function to be minimized took into account the efficiency of each of the water plants and the total flow to be treated in the distribution. To solve this problem, the two-phase simplex algorithm was used. This was implemented in the controllers and runs periodically. In this way, there will always be an optimum distribution in the water plants. As a result of this implementation, the quality of water delivered by the distribution system and the autonomy of this process were increased. On the other hand, the variability in the SKIM Tank level decreased.